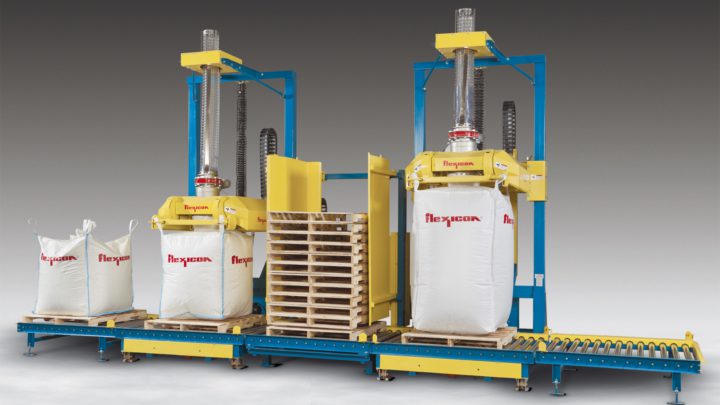
When a filling cycle is initiated by push button or contact closure, pallet dispenser forks lower the stack of pallets onto the roller conveyor, withdraw from the bottom pallet and raise the remaining pallets. This allows the roller conveyor equipped with photoelectric sensors to move the dispensed pallet into position below the filling station.
The bag connection frame of the Swing-Down fill heads lower and then pivot to a vertical position, allowing an operator at floor level to safely and quickly attach bag straps to automated latches, slide the bag spout over an inflatable spout seal, and press a spout seal inflation button. The system then automatically pivots the bag connection frame back to horizontal, raises the entire fill head, inflates the bag to remove creases, fills the bag at a high rate, finishes filling accurately at dribble feed rate, deflates the spout seal, releases the bag loops, raises the fill head to disengage the spout, rolls the bag out of the filling area, and rolls a new pallet into place to begin another cycle.
To maintain a clean safer working environment an annular gap inside of the fill head spout directs displaced air and dust during the filling operation to a single point connection.
All system components are available constructed to industrial, food, dairy and pharmaceutical standards.
The new Dual Bulk Bag Filling system is available with a Flexicon mechanical or pneumatic material delivery system ready for integration with the user’s upstream process equipment or other material source.
The company also manufactures bulk bag unloaders, bulk bag conditioners, bag dump stations, drum/box/container dumpers, weigh batching and blending systems, and engineered plant-wide bulk handling systems with automated controls.
Contact Alan Walton: sales@flexicon.co.uk