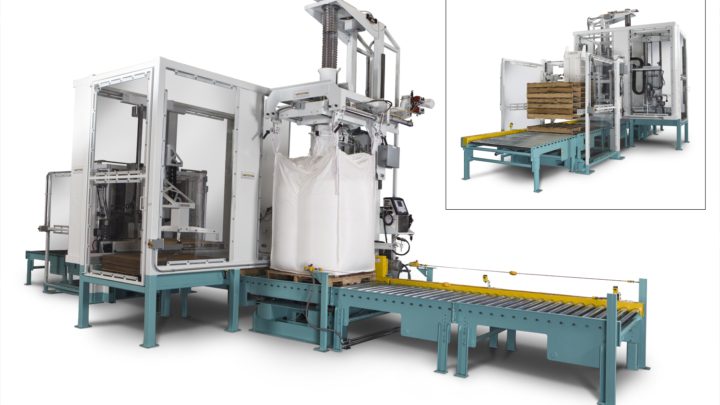
The complete process sequence, including pallet/base supply, slipsheet pick-and-placement, bulk material infeed, packaged contents isolated densification, NTEP-certified weighing and finished-package accumulation conveyance, operates on paired, process-specific structural framework chassis with all automation and control functions centralised to a single, menu-driven HMI. This is designed to enable standardised and system-wide data reporting.
In the pallet dispenser phase manual handling of pallets is eliminated. The pallet stack, delivered by forklift, is conveyed into the dispenser where the stack is automatically formed and each pallet is aligned and staged to advance into the slipsheet dispenser. The slipsheet dispenser magazine can hold up to 2,500 lbs of sheet.
The bulk bag filling stage of this NBE bulk packaging system uses a cantilevered fill head/bag hanger carriage design with pneumatic actions to bring the fill head and rear bag hooks to well within the operator’s reach; eliminating the need for the operator to step or lean into the equipment.
A physical ergonomic design maintains optimal operator posture for safe operation. The 8GPM hydraulic lift carriage lifts bag capacities up to 4,500lbs; exceeding the lift speed and capacity of ball screw designs. The NTEP-certified hang-weigh system provides valid, accurate, and repeatable weighing of bulk bags to an accuracy of +/-0.05 percent of the 4,500lb bag weight. A bulk bag densification platform uses 3Gs of high speed, low intensity vibration to settle material in the bag to a dense, stable, and safe load. The vibratory action is isolated from the deck and focused on the bulk package to ensure precise package weight accuracy.