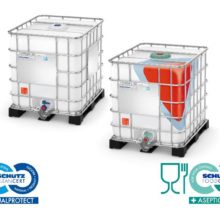
The Ecobulk Foodcert + Aseptic fully meets the specific requirements in the food, pharmaceuticals and toiletries industries; it effectively excludes contamination risks along the entire supply chain, extends the shelf-life of the filling products and ensures consistent quality from filling to emptying. All of these benefits have been achieved by including a special component in this IBC model: an integrated liner which is certified in accordance with the FSSC 22000 industry standard that guarantees the highest food safety. The liner is made of high quality LDPE film which unfolds and aligns itself automatically in the inner bottle during filling. It lowers the risk of leaking, increases cleanliness and also has an EVOH permeation barrier against oxygen. The gradual unfolding of the liner also means that contact between the filling product and the ambient atmosphere is kept to a minimum. The result is 99 percent less exposure to oxygen than in a standard IBC!
Sterile IBC reduces risks
As a special measure to mitigate microbial contamination the integrated liner and valves are sterilised by gamma radiation with an average dose of at least 15 kGray. The IBC inner bottle also forms a highly effective, independent barrier against leakage, even if the integrated liner is damaged, thus providing double protection for the filling product. For maximum safety, cleanliness and ease of use, the IBC is delivered “ready to fill”, so the packaging does not require steam sterilisation of the inner bottle or time-consuming inliner assembly to save time and money. The Ecobulk Foodcert Aseptic can be filled and emptied on all conventional lines, including with pump systems and under aseptic conditions.
Ecobulk Cleancert + Dualprotect
Schütz also offers the innovative liner system for industries that handle highly sensitive non-food products. This Ecobulk version is the Cleancert + Dualprotect. The name says it all: this IBC version also offers double protection for filling products thanks to the integrated liner. The IBC features a leakproof inner bottle, thus effectively avoiding leaks even if the liner is damaged. The new packaging solution for technically demanding products is extra safe and, because it is delivered “ready-to-fill”, is also exceptionally user-friendly. A good example of an application field is the adhesives industry; when exposed to oxygen, the majority of these products react by forming a film or even starting to cure. The integrated liner minimises oxygen contact during filling as well as inside the packaging, thus preventing the filling product against oxidation extending the product shelf-life and making it easier to discharge.
Two new models with many advantages
In most multi-use systems there is a significant risk of accidental contamination due to product residues. This is ruled out in the two new models. Filling into the integrated liner minimises the general risk of contamination and there is minimal risk of the filling product coming into contact with condensate, which can form inside the inner bottle. The liner’s oxygen barrier provides additional protection against oxidation, vitamin depletion and microbial contamination and, unlike other container types, there is no need for nitrogen blanketing. UN approval for hazardous goods transport also applies to the IBC version with a liner.
Easy handling – from filling to discharge
Ecobulk can be filled via the IBC’s standard outlet valve or from above via a filler nozzle which is attached to the liner and can be fitted to different bungs as required. For aseptic applications, both the outlet fitting and the bung used at the filler nozzle can be steam sterilised. The integrated liner unfolds on its own as it is filled. The air in the inner bottle is vented by opening the screw cap. Optionally, the container can also be filled from above using the filling nozzle in the liner.
As a rule, the container is emptied gravimetrically though the outlet valve which is securely and rigidly attached to the IBC inner bottle. For liquids with a watery consistency, this method achieves an almost residual free emptying. For more viscous filling products the cap nut can be loosened and the liner and the outlet valve can be carefully pulled out of the container in order to empty it completely. Once the IBC has been emptied, the Schütz Ticket Service offers a worldwide administrative-free collection service and then reconditions both the IBC and inner bottle in an environmentally-friendly process – giving this innovative system both great economic and ecological benefits.