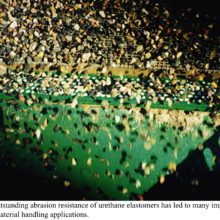
In such cases, the bare structure of the equipment may not be adequately wear resistant and even traditional steel or rubber protective liners may insufficiently control the abrasion. This can pose a risk of costly spillage through holes and gaps, along with production downtime for repair and clean up. For such applications, sheets made from urethane (short for polyurethane) provide far better wear resistance than more traditional options such as rubber or steel (both AR400 and AR450 plate). Urethanes are cost-effective, dependable elastomers that combine some of the performance advantages of high-tech metals, ceramics, and plastics, along with the resiliency of rubber.
Because urethanes also offer significantly less friction than rubber, this not only helps to reduce wear in contact with rough materials like aggregate and sand, but also improves equipment cleanability between wet batches, which enhances productivity. Now this “tougher than steel” liner can be made even more durable with embedded ceramic tiles. It can also be cut from full sheets of various sizes to fit the contours and shapes of high contact areas, so it can easily be welded or bolted to provide extreme wear protection wherever it is required. While such liners can be cut to fit and installed onsite, custom liners made to fit more complex configurations can increase reliability, simplify installation, and further reduce production downtime.
Extreme Wear Resistance
The outstanding abrasion resistance of urethane elastomers has led to many important bulk material handling applications.
“In plants that handle bulk materials, like concrete ready mix facilities, where severe wear is a problem, special urethane formulations like Kryptane can last several times longer than steel or rubber, which reduces production downtime, replacement cost, and labor for change out,” says Jesse Roberge, a concrete industry product specialist at Argonics, one of the U.S.’s largest producers of wear resistant urethane products. Kryptane, an extremely wear-resistant material designed by the company for applications where abrasion, sliding, or impact occurs regularly, is often used in a wide range of batch plant applications including as drum, chute, bin, hopper, and conveyor liners. According to Roberge, different applications require different thicknesses of urethane. “For wet batch central mix drums, we recommend a 1” thick liner, which can last 5 to 10 years,” says Roberge. “In fact, some wear liner manufacturers offer a warranty of several years or based on the yardage put through a drum.”
To most effectively control extreme wear, such as for feed chutes, discharge chutes, and turn-heads, Roberge recommends the use of liners that actually embed ceramics into the urethane. “Urethane with embedded ceramics can be optimized to resist not only sliding abrasion, but also impact, or various combinations of the two,” says Roberge. “This approach can last up to 10 times longer than steel or rubber alone, and up to 4 times longer than urethane alone.” To resist liner degradation in hot, humid climates and further extend liner life, he also advises the use of an ether urethane formulation, instead of a typical ester formulation.
Roberge points to another benefit of the urethane. Compared to steel liners, the urethane significantly reduces the noise level at the concrete plant. “When all this rock and aggregate falls onto metal, it can be quite loud, particularly if it is in an enclosed building,” he says. “Because the urethane has natural resilience, it deadens the sound quite a bit and makes conversation easier.”
The process for customizing liners is quite simple for plant managers and the OEMs that manufacture such equipment. According to Roberge, the customer typically provides a sketch, drawing, or photo of the bulk handling equipment to be lined, along with dimensions and notes. The wear liner producer then finishes the drawings and provides a quote. If the customer approves, the liner is completed, shipped, and is ready for installation when received. Whether used as standard or custom liners, urethane’s extreme wear resistance can offer plant operators, design engineers and equipment manufacturers extended equipment life and trouble-free handling of bulk aggregate and sand materials. This improves safety, production, and the bottom line.