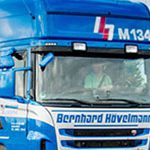
New paths in the family business: telematics, automation and digitalisation
Hövelmann Logistik, a family business, was founded in 1945 in the town of Rees am Niederrhein, where its head office is still located today. The company has also been based in Saxony-Anhalt since 1991. Its location in Haldensleben, which occupies an area of approximately 50,000 m², is now the company’s biggest. With more than 600 employees and some 230 trucks, Hövelmann Logistik is a medium-sized player in the logistics sector in Germany. When it comes to digitalisation, the company is proceeding along the path to “Logistics 4.0” on an innovative and forward-looking basis.
Since 2010, all of its trucks have gradually been equipped with telematics. A high-precision system for positioning, navigation and communication is used, which allows for efficient fleet management. Real-time data on positioning, traffic flow, driving and rest times and driving behaviour are registered and analysed. This reduces response times considerably.
The data gathered on driving style and driving behaviour are used for driver training, a task for which Hövelmann has hired two driver trainers. “If our drivers use one litre less of fuel per 100 kilometres as a result of these measures, with over 27 million kilometres per year, that makes a big difference,” says Maslock.
At Hövelmann Logistik, scheduling plans based on paper documentation are a thing of the past. All trips are digitally planned with a freight forwarding software package and the orders are transferred directly to the vehicle via telematics. Visual inspection of driving licences has also been simplified using an RFID chip, provided that the drivers have given their consent.
In the warehouse, the processes are optimised with digital help. A “pick by voice storage system” simplifies the order picking by allowing the employee to receive the information via headphones without having to operate a paper or scanner.
Digitalisation requires willpower
As successful as the individual measures have been in terms of their impact the success of the company, their implementation has also come at a cost. “It is certainly true that digitalisation strengthens the control mechanisms,” emphasizes Maslock. “But with the added value for the employees, such as the payment of bonuses when our targets are reached, we have been able to convince our employees of the benefits of digitalisation and to inspire them.”
As of 4 June, the company will be exhibiting at the joint stand for the federal state of Saxony-Anhalt at the transport logistic event in Munich, the leading international trade fair for logistics, mobility, IT and supply chain management.
*Source: the German Federal Association for Logistics e.V. (BVL) https://www.bvl.de/service/zahlen-daten-fakten/umsatz-und-beschaeftigung