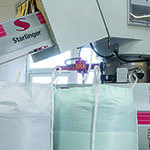
The challenge in the recycling of big bags is that they come in different forms: with or without polyethylene liner, coated or uncoated, and with loops and seams consisting of different kinds of plastic. Therefore, the first step in creating a circular economy for big bags is “design for recycling”; this means that the big bags are designed in such a way that they can easily be recycled and processed. The second important step is creating a material passport in which the entire life cycle of the big bags is documented, from the first filling and the filled product up to the materials used in big bag production.
In cooperation with the renowned big bag manufacturers Louis Blockx and LC Packaging, Starlinger has simulated this closed loop and produced new big bags with a high content of recycled PP. Tests show that these “rPP” big bags show the same quality as big bags made from virgin material in terms of tensile strength, weight, and safety factor. These promising results make Starlinger a hot candidate for this year’s Plastics Recycling Awards Europe. The award winners will be announced on 26 March, during the second day of the Plastics Recycling Show Europe taking place at the RAI Amsterdam.