
Supplied by Freeway Fleet Systems, engineers and technicians are equipped with rugged tablets for digitally recording time and work activity. Synchronised in real-time, a Freeway central asset maintenance system, the mobile devices and management software give Abbey 24/7 visibility of the status of all maintenance work and costs associated with parts and labour.
Abbey had previously implemented a system to manage compliance and maintenance but with the business expanding, a more integrated and comprehensive system was required that would provide better management information and a platform for future expansion.
Digital working in your hands
A key feature of Freeway is that it extends digital working into the hands of staff in the workshop and Abbey is equipping technicians with tablets to digitally record their timesheets, inspections and job cards.
Abbey Logistics Group operates almost 1,000 liquid and powder trucks and tankers. Having recently invested more than £4.5 million on new vehicles and trailers, Abbey maintains a tight control of vehicle maintenance to ensure high safety standards and avoid breakdowns.
“Our previous system was fine for monitoring vehicle and parts costings but that was only giving us half the picture. We found that we were missing information on, arguably our most important single asset, labour,” says Paul Jamieson, head of finance at Abbey Logistics Group.
“With Freeway’s tablets in the workshop, we have visibility of all work in real-time allowing better co-ordination with the workforce, improving uptime. We also gain vital insights such as an accurate cost allocation per asset. That allows us to make properly informed decisions on how to improve the way we work.”
End-to-end solution for larger fleets
Freeway provides a complete end-to-end solution ideally suited to operators with larger fleets with one or multiple workshops. As well as the core functions of managing services, inspections, defects and compliance, Abbey are implementing Freeway for managing stores for digital parts issuing and stock control, with automated replenishment on impress stock.
Abbey also uses Freeway’s driver app so drivers can use their mobiles to record their walk-around safety checks. This gives the workshop immediate visibility of any issues so decisions can be made immediately on the urgency on the rectification of any reported defect.
“Crucially, Freeway joins up the dots between the fleet team, the operations team and drivers,” says Jamieson. For example, the introduction of a live, paperless defect system is one way we can ensure the fleet is proactively maintained and 100 per cent compliant at all times.”
“Freeway is brilliant as it gives us a single point of access to all the information we need; it is fully integrated and represents a significant step up in our system capability. It is particularly good at providing an insight into our performance and costs, down to individual parts and people, so we can be fully informed when making business decisions,” Jamieson adds.
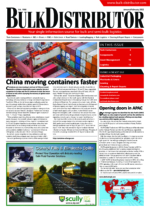