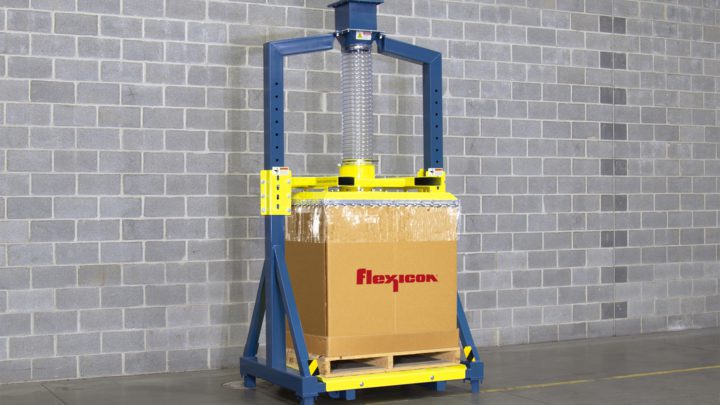
The unit’s fill head can be raised or lowered using a forklift and secured with clevis pins to minimise the clearance between the rectangular dust hood and the opening of IBCs ranging from 1220 to 1980 mm tall.
A fill head port can be vented to a filter sock to contain displaced dust, or to a central bag house that causes a clear flexible skirt to vacuum-seal against the container’s exterior, increasing dust containment effectiveness.
Performance can be enhanced by a vibratory deck to densify and stabilise the material during filling, and/or load cells that signal a PLC when to stop the flow of material by stopping a conveyor or closing a rotary valve or slide gate once a programmed weight is gained.
Rated for loads up to 2945 kg, the frame is offered in carbon steel with durable industrial coating, with stainless steel material contact surfaces, or in all-stainless construction to industrial or sanitary standards.
It can be integrated with Flexicon mechanical or pneumatic conveying systems, or the user’s upstream process equipment or storage vessels.
Flexicon also manufacture dust-free IBC tippers, as well as bulk bag fillers, drum fillers, bulk bag dischargers, flexible screw conveyors, tubular cable conveyors, pneumatic conveying systems, bulk bag conditioners, bag dump stations, weigh batching and blending systems, and engineered plant-wide bulk handling systems with automated controls.