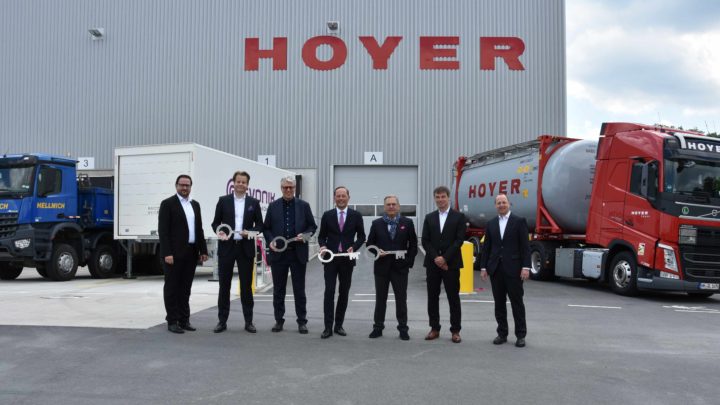
Conceptually planned in detail with the customer, the logistics warehouse represents the high demands of the logistics company specialising in liquid goods, in the areas of safety, customer orientation, quality and efficiency.
With Supply Chain Solutions, the HOYER Group has at its disposal a dedicated team of experts for on-site and off-site solutions to handle the products of the chemical and gas industries.
The HOYER Group is well-known as one of the leading specialists in the transport and handling of liquid dangerous goods.
With Supply Chain Solutions, the logistics company provides customers in the chemical and gas industries with committed expertise in on-site and warehouse logistics. Even in this business field, logistics solutions tailored to customer requirements are a matter of course for HOYER.
Intensive co-operation for delivery
Operated by the HOYER Group, the new logistics centre in Essen is the result of intensive cooperation between the logistics provider and the speciality chemicals company Evonik.
The facility, with technologically state-of-the-art equipment, also meets the highest safety standards. Goods receipt, storage and order picking processes are semi- and fully-automatically implemented as far as possible. For example, goods flow has been digitalised via the seamless tracking of SSCC18 pallet numbers. This increases efficiency in processing and personnel deployment, thus simplifying and speeding up the complex value-added chain of the chemical industry: a critical success factor in this sector.
Björn Schniederkötter, CEO of the HOYER Group, said: “We understand the challenges our customers face – and support them with customised solutions to meet these successfully. Safety and efficiency set the parameters in this respect.
“We welcome the fact that Evonik shares our concepts of value. In addition to a dedicated protection and prevention concept, the new location inspires confidence through efficient work lines, state-of-the-art equipment, intelligent software and an energy-efficient plant.”
The largest international finished product
The new logistics centre is Evonik’s largest international finished product warehouse for palletised goods, and is also highly modern: it is the first time HOYER has used driverless transport systems in a warehouse. In addition, there are semi-automatic storage and retrieval devices, with the option of driving forward full automation of the warehouse.
The HOYER Group sends a clear signal for progress, digitalisation and modern logistics along the entire supply chain. The excellently trained staff will continue to guarantee smooth operation. They are responsible for the safe, timely execution of tasks, and ensure that HOYER keeps its promise to customers. All the logistics processes meet the highest standards in terms of safety, quality and efficiency.
HOYER coordinated the approach routes and processes in detail with Evonik. The largest manufacturing industrial company in Essen transfers various raw materials and finished products from the adjacent site across plant boundaries to the HOYER logistics centre, where containers are stored centrally and order-picked for onward transport.
The ramp-up in volume terms to the target filling level will be achieved in the second half of 2022. The warehouse offers 27,000 pallet spaces on 19,000 square metres of floor space for 18,000 tonnes of products, which are stored there safely and properly with the help of software.
Saving three million tonne-kilometres of road transports
The precise planning and direct connection between production and storage facilities contribute to Evonik’s climate targets: the location of the logistics centre alone saves the company around 3 million tonne-kilometres of road transport – equivalent to around 3,000 truck journeys. This saves a total of 210 tonnes of CO2 per year. In the warehouse itself, a modern electrified fleet of industrial trucks and the energy saved by equipping the site with the latest LED lighting to contribute to sustainability.