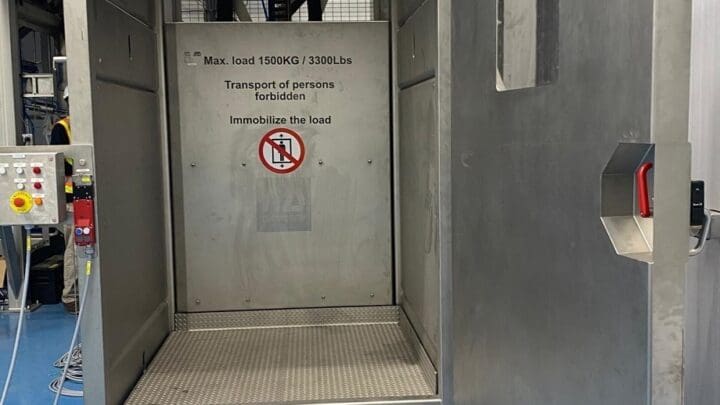
The company says the lift saves space, accelerates work processes, and minimises safety risks through automated vertical movement of raw materials and goods. The choice of stainless steel was to meet strict hygienic standards as Dinnissen supplies equipment to the food industry.
The idea emerged during a project in the United States. Dinnissen built two mixing lines for a multinational in dietary supplements (collagen powder).
Specialists Frans Bakker and Melvin van der Hilst noticed that the design was not sufficiently safe. Pallets with raw materials had to be placed on a platform at a height of 8m, posing significant risks. Back in the Netherlands, a safer solution was developed: a lift to elevate the pallets with raw materials safely.
The idea was immediately well received by the client. A search began for a supplier capable of delivering fully stainless steel lifts without hydraulics, in line with stringent hygienic requirements.
When no suitable supplier could be found, Dinnissen decided to design and build the lifts itself, fully tailored to the client’s needs.
The lift uses a mechanical belt drive instead of hydraulics. This not only enhances hygiene but also increases system reliability and durability.
It can be built in various heights and support lifting capacities ranging from 500 to 2,000kg.