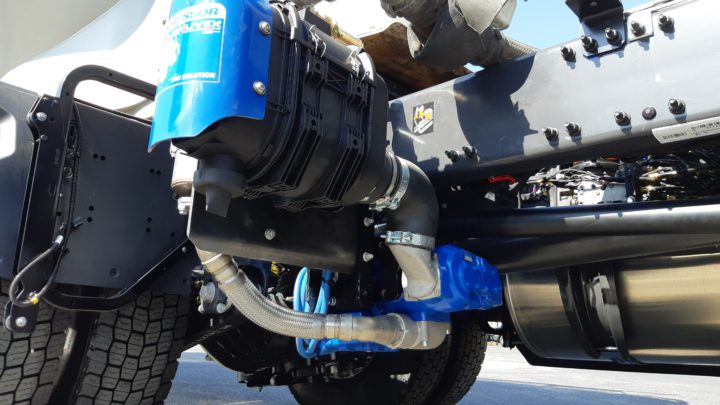
In the bulk transport industry, less leads to more. In recent years, trucks and their transport containers have become lighter, be it through thinner container materials, smaller containers or less heavy vehicles.
These changes have occurred across the industry as a way for companies to get more out of their operations. If a truck and the container weigh less, they can improve their fuel efficiency and operational costs, while also slightly increasing their payload.
But transport companies are not simply optimising to save on costs either. In the European market, recent regulations, such as Euro 6, have created stricter vehicle standards.
These standards began in 1992 (Euro 1) and have evolved to their current iteration, which was established in 2015. The Euro 6 emissions standards are the strictest of the bunch, and address real-world NOx and PM emissions from diesel trucks with changes to the heavy-duty vehicle test procedures, according to the International Council on Clean Transportation.
Another part of this mix is the apparatus that aids the bulk transport industry in European markets – screw compressors. With the latest emissions standards and the trend to go lighter and be more cost and fuel-efficient, screw compressors must also adapt to these requirements to ensure successful adoption in future bulk transport operations.
This article provides the essential elements needed for screw compressors to become the preferred equipment choice in the bulk transport industry.
The lighter side
With bulk transport operators making weight (and less of it) a priority, screw compressors will need to be lighter to ensure transport vehicles don’t add unnecessarily bulky equipment that will impact their efficiency. Lighter screw compressors, especially for these applications, are possible.
One example is the MX12 Screw Compressor from Mouvex, based in Auxerre, France, a product brand of PSG. The MX12 compressor weighs only 110kg, which allows it to operate on the transport vehicle without impacting its efficiency.
Another important facet for transport vehicles, which put a heavy premium on space, is equipment footprint. Equipment that takes up less space frees it up for additional product storage which equates to a larger payload between transports.
The MX12 also serves as an example of a compressor that has a small footprint. It measures 541mm to 569mm long, 346mm wide and 451mm tall. That footprint allows the MX12 and similar screw compressors to fit on nearly all vehicle chassis without sacrificing space for other equipment or, most important, bulk product.
Another valuable attribute for a screw compressor with a compact footprint and low weight is a design that allows it to fit in nearly any space without compromise. The most optimal design for a screw compressor in these applications is modular. With that kind of design, operators can install the screw compressor easily in a variety of locations. Additionally, a modular design makes it simple for operators to repair, modify or upgrade the screw compressor as needed.
Consistent performance
A compact, lightweight, modular screw compressor checks the proper boxes for space, but all of these attributes are moot without reliable performance. Screw compressors in bulk transport applications need to provide consistent, reliable performance to help offload a variety of bulk products, such as cement, sand, gravel, plastic pellets, flour, calcium and animal food.
Important performance attributes include a fast flow rate, robust pressure and a low inlet speed. A screw compressor that can deliver flow rates up to 1,130 cbm/hr) will substantially reduce the time it takes to offload product. For example, if a bulk load requires an hour to offload using a standard screw compressor, having equipment with a high flow rate can do the same job 10-30 minutes faster. Having a faster offload process allows operators to finish jobs faster and unload more bulk products every day.
With a fast flow rate achieved, a screw compressor also needs to reach and sustain enough air pressure to ensure the integrity of the bulk product delivery through the process. A screw compressor that can reach and maintain 2 bar of air pressure is capable of handling bulk loads of all sizes and consistencies, be it gravel or plastic pellets or finer materials such as sand and flour.
Another essential attribute is low inlet speed. The importance of fuel efficiency has already been discussed, and having a low inlet speed provides operators with a screw compressor that will keep fuel costs and consumption low.
Other considerations
There are a variety of other features, beyond the essential ones, that bode well for screw compressors in bulk transport applications. One common problem for this equipment in these operations is overheating during operation. This problem will cause a screw compressor to stall, which will hamper the entire offloading procedure. To remedy this, screw compressors should incorporate an oil radiator into the apparatus. Doing so will regulate the screw compressor’s internal temperature so that it won’t stall during operation, which means it won’t be prone to overheating.
Another consideration is selecting a screw compressor with an anti-vibration design. Compressors of all variations will vibrate as part of their functionality. Vibration is a by-product of compressors, leading many operators to use clamps or mounting brackets to reduce it to manageable levels. The problem with vibration, though, is it causes stress to the compressor itself and can wear it down over time.
While clamps or similar components can reduce vibration, finding a screw compressor with an optimised design, especially in bulk transport applications, is ideal to ensure the longevity and reliability of the components, leading to less downtime throughout its lifetime.
Additional considerations, depending on the specific application, include:
• For construction materials, such as cement, having an integrated PTO module on the screw compressor will make it compatible with most European truck frames without the need for torque limiters, gimbals or holders.
• For situations where space is confided beyond typical standards, there are screw compressors with even smaller footprints – 549 x 348 x 280 mm – that weigh as little as 94 kg.
• For dry bulk applications with extremely low atmospheric temperatures (-30degC), a screw compressor composed of cast iron or hardened steel will ensure proper functionality as well as good material compatibility.
• For liquid cargo delivery, screw compressors should have protectants on their body and screws, and have all exterior components constructed from stainless steel to ensure better compatibility with a broad range of chemicals. The components also provide additional protection against abrasion and corrosion in this type of application.
Conclusion
The demands for stricter emission requirements and lighter and more compact vehicles likely won’t lose momentum in the near or distant future. Space on these vehicles is at a premium for a reason and essential equipment, such as screw compressors, should not be sacrificed for less effective technology. The Mouvex MX12 is an example of a screw compressor that provides the footprint and performance needed to help operators with their bulk transport needs without the need to compromise on efficiency or functionality.
Christophe Jovani is the EMEA – marketing communications manager for Mouvex and PSG. Mouvex is a product brand of PSG, a Dover company, Oakbrook Terrace, IL, USA
This article is from the November/December issue of Bulk Distributor magazine. To receive a digital copy of the magazine as well as our monthly newsletter, sign up here.
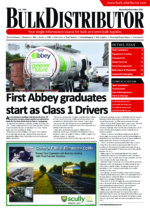