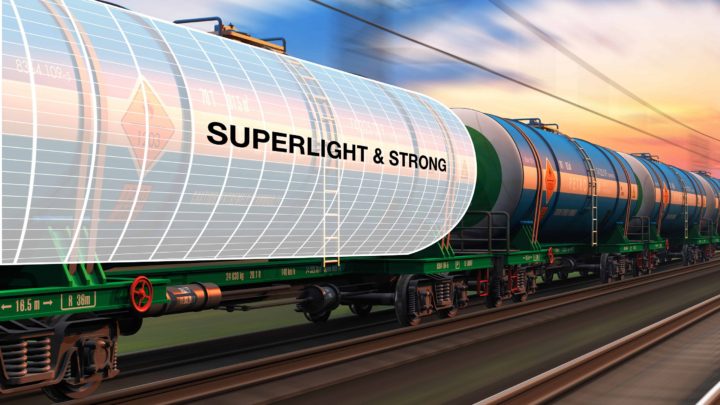
Fibre reinforced plastics manufacturer Lamilux Composites says that cladding a container with Lamilux X-treme glass-fibre reinforced plastic permanently protects the representative shell from UV, weather and mechanical effects.
Lamilux X-treme is a composite material with the maximum possible content of reinforcement fibres in a highly elastic epoxy resin matrix. The shock-resistant material reduces maintenance and repair costs, thus reducing container downtime.
Tank containers of all kinds are also subjected to very high mechanical loads during loading and transport; whether on a cargo ship, trains or trucks.
Even under the toughest conditions, Lamilux X-treme remains visually appealing and maximises the durability of the life of the entire structure, the makers say. The operator also saves running costs for its fleet, as the tank has a significantly lower deadweight than ones with conventional exterior shells.
50% lighter thank other materials
Lamilux X-treme and its carbon version absorb any load and tension forces on sandwich panels with their large-scale use in a wide variety of applications, making the whole structure resistant to torsion. This becomes clear when the carbon-fibre-reinforced polymer is compared with other materials used as sandwich face sheets. It is up to 50 percent lighter with a tensile strength three or four times greater than steel or aluminium.
The low thermal expansion ensures that large structural components can be produced without bubbles or distortions emerging in the long term. The low thermal conductivity in products and the consequent optimised insulation in cooling transport containers make powerful arguments for the material’s use in refrigerated trucks.
However, all such properties are not of any use to the commercial vehicle industry if the material is unable to take mechanical stress loads caused by shock and impact. X-treme products not only withstand such loads, but usually resist them in a way that completely prevents major damage and downtimes due to repairs in most cases. The material even manages to hold fast during hail storms and adverse weather conditions, making it ideal for both body interiors and exteriors.
Lamilux composites are produced in a continuous, automated production process. The separate production lines guarantee minimum delivery periods while providing consistently optimum quality which can be reproduced at any time. The product range can be manufactured in widths up to 3m, while the length of sheets or rolls are tailored to customer requirements.
Setting global standards
Thanks to the maximum possible content of reinforcement fibres, equal to approximately 70 percent by weight, and perfect bonding with the high-strength epoxy resin matrix, enormous tensile strengths can be achieved which are more than twice that of steel.
X-treme thus achieves three times the tensile strength of other most other cladding materials and exceeds the strength and rigidity values of most materials many times over, the company claims.
Now a member of ITCO, Lamilux Composites says it is setting global standards for the transport of tank containers and is thus actively shaping the future of the tank container industry.
“We are very pleased to have become a member of ITCO in February last year and to be able to work with the organisation on its mission to promote and present tank containers as a safe, cost-effective and flexible means of transport. Here we can support the organisation especially in technological developments in the interest of quality and safety,” said Sascha Oswald, head of product management.
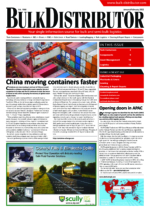