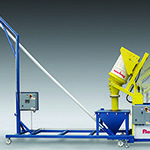
The system’s TIP-TITE® Drum Tipper accommodates drums from 114 to 208 litres, weighing up to 340 kg and measuring 90 to 120 cm in height. Mounted on a mobile frame with quick-action floor jacks, it raises the drum hydraulically to form a dust-tight seal between the rim of a drum and the underside of the discharge cone. A separate hydraulic cylinder tips the platform-hood assembly and drum, stopping at dump angles of 45, 60 or 90 degrees with a motion-dampening feature. The vertically-oriented cone mates with a gasketed inlet port fitted to the hopper of the system’s flexible screw conveyor, and to any low profile equipment throughout the plant. A pneumatically-actuated slide gate valve prevents material flow until the discharge cone has been properly seated in the gasketed receiving ring.
The mobile FLEXICON® screw conveyor, which can operate independently or when mated to the drum tipper, can feed material to elevated process equipment and storage vessels. The only moving part contacting material is a rugged inner screw which can move both free- and non-free-flowing materials with no separation of blended products. The screw is driven beyond the point of discharge, preventing material contact with seals or bearings. Removal of the hopper lid allows manual dumping and feeding from upstream equipment.
Flexibility of the tipper and conveyor to handle a diversity of materials independently or in tandem throughout the plant enables the system to satisfy a range of current and future requirements, according to the manufacturer.
Ready to plug in and run, it is constructed of carbon steel with a durable industrial finish, and is available with stainless steel material contact surfaces or in all-stainless construction, finished to food, dairy, pharmaceutical or industrial standards.