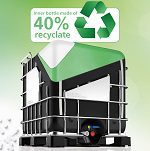
Ecological packaging as a comprehensive concept
The entire life cycle of Schütz IBCs packaging is geared towards ensuring maximum environmental friendliness. During reconditioning as part of the Schütz Ticket Service, the inner bottles of collected IBCs are removed from the steel grid and treated in a complex recycling process during which they are ground, cleaned and finally regranulated.
Special degassing extruders ensure a low-odour, homogeneous quality. The company uses the HDPE recyclate obtained in a closed cycle: 100 per cent flows back into the internal production of plastic packaging components, including corner protectors and plastic pallets. This is why Schütz IBCs have always had an exceptionally high proportion of recycled material. Depending on the type of pallet, the proportion is between 36 and 55 percent of the plastic in the entire IBC.
CO2 savings per IBC
The IBC container in the innovative Green Layer design contains 40 percent recycled material alone. This corresponds to an additional CO2 saving of at least eight kilograms per IBC. The recycled HDPE is extruded only into the middle layer of the container. The inner and outer layers are made of virgin HDPE material. This way, Schütz ensures that both the filling product and the environment only come into direct contact with virgin material, making a significant contribution to protecting the quality of the filling product. Equipped with a full-plastic pallet, the total content of recycled plastic in this particular IBC model is as high as 73 percent.
Sustainable IBCs and PE drums with UN approvals
The new Schütz IBCs have UN approval and are therefore also suitable for a wide range of dangerous goods applications. The new containers also impress with their uniform appearance. The outer layer is completely black, thus avoiding colour variations that often occur when recycled material is used in IBC inner bottles. Transparent view stripes enable the user to monitor the filling level in Green Layer IBCs at all times. Schütz also uses multi-layer extrusion for the production of drums, combining maximum safety with a maximum content of recycled plastic. The F1 tight-head drum in 220l and the S-DS1 open-head drums in sizes 30l to 220l are also produced as Green Layer models using the three-layer extrusion blow-moulding process with recycled HDPE in the middle layer. The recycled content here accounts for 40 per cent of the drum body and the entire product range has dangerous goods approvals.
Market launch in Europe with pilot projects
With the European Green Deal and the Action Plan for the Circular Economy, the European Union has defined the goals and framework conditions for resource-saving economic growth. The future legal requirements for the use of recyclate in packaging are already met by the new Green Layer products. In order to ensure a constant supply of IBCs and drums with recycled plastic material, Schütz emphasises how important it is for customers and returners of used industrial packaging to actively cooperate. A corresponding supply security can only be guaranteed, if there is a sufficient supply of recyclate from the Schütz Ticket Service, the global system for the reconditioning and recycling of industrial packaging by Schütz. The market launch of the Green Layer products therefore requires close coordination with customers and is initially limited to Europe, where pilot projects have been successfully launched. Future expansion into other regions is possible and intended thanks to the global production network of Schütz with state-of-the-art multilayer extrusion blow moulding equipment.