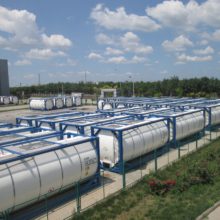
However, stress corrosion crack (SCC) has been observed on the vessel head of tank containers in recent years and has attracted much attention from researchers. This kind of SCC cannot be easily detected until the leakage penetrates the insulation, or until a tank container undergoes the next hydrostatic test, therefore it is difficult to prevent in advance.
Together with the R&D faculty of Tianjin University, MCC Tank has recently developed an experimental method. By using, the behaviour of the SCC on the vessel head can be investigated; therefore the inner factors that cause SCCs can be determined. Hence an extra facility is applied during the process of tank manufacturing to eliminate the inner factors theoretically.
MCC Tank is a wholly owned subsidiary of Metallurgical Corporation of China (MCC) which is a Fortune Global 500 company (#302 in Y2013). MCC is biggest Chinese metallurgical engineering contractor and provider of technological upgrading and reconstruction services in metallurgical engineering with a complete industrial chain in ferrous and non-ferrous metallurgy. MCC Tank started tank container manufacturing since January 2013 with an annual production capacity of 5,000 TEU. The workshop is located in Hangu district of Tianjin, 30km from port Xingang and 180km from Beijing capital airport.
The experimental team of MCC Tank investigated dozens of tank containers with leakage and the results indicate that most SCCs occur within the 50mm radius from the heat affected zone of girth weld on the vessel head of tank containers.
Further comparative experiments were carried out on specimens with SCC, new vessel head specimens and original stainless steel specimens by the team. In order to determine the type and inner factors of SCC, the microstructure, the composition on the surface of crevice and the elements of the remaining corrosive substance were analysed using an optical microscope (OM), scanning electron microscopy (SEM) and X-ray diffraction. The results of experiments indicate that there are three main factors causing SCC as following:
- There is a Cr-rich phase precipitating from the austenitic stainless steel (Stainless Steel 316L) during the service life. Cr does not diffuse easily thus the areas around the second phase become Cr-depleted and are sensitive to corrosion.
- With exposure to chloride ions, pitting and inter-granular corrosion will appear in Cr-depleted regions, which leads to crevice corrosion under the influence of residual stress.
- The decrease of Cr and segregation of S element on the tip of the crevice increase the corrosion susceptibility of 316L SS.
In other words, there are three prerequisite conditions for SCC on austenitic stainless steel 316L:
1) Nature of chemical transport: chance of coming into contact with a corrosive substance, eg, chloride ions
2) Nature of SS 316L: Microstructure susceptible to SCC – nature of SS 316L
3) During manufacturing process: tensile stress
SCC occurs under the combined effect of the above three prerequisite conditions, and the absence of each of the three conditions can hinder the stress corrosion cracking. As a tank manufacturer, MCC Tank aims to eliminate the tensile stress accumulated from applied stress or residual stress caused by heat treatment. This can be achieved by converting the tensile stress into compressive stress during tank manufacturing process. An additional ultrasonic facility with an efficiency of 9m per minute is used in the tank manufacturer’s workshop which can make the conversion.
So far the data show that the chance of SCC on tank containers can be reduced by up to 10 times by the new MCC technology which is patent-protected.
For more detailed information go to:
www.mcctank.com