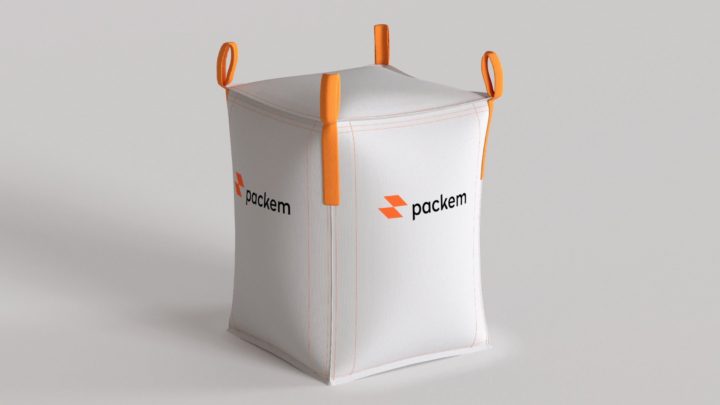
“This new facility in Asia will take Packem to global markets that are already served today by Umasree, in PP bags, especially the United States, Canada and Europe,” said Eduardo Santos Neto, CEO of Packem. “We have been Umasree’s business partners for over 10 years and it was this relationship of trust that enabled the joint-venture and the joint investment of US$15 million in the new facility, being 51 percent Packem and 49 percent Umasree.”
The transaction was assisted by MNSS Advisors, which acted as financial, legal and tax advisor to Umasree, and by law firm Trilegal, which handled Packem’s interests.
The future PET/PCR big bag facility is expected to create about 700 new jobs in India, which is the largest producer and exporter of big bags in the world. “Our rPET big bag will bring great environmental and social benefits to India, in addition to direct jobs. It is estimated that every ton of recycled plastic will create three local jobs for the collection and recycling industry. In addition, our project will create local demand for post-consumer PET bottles, with positive impact for oceans, rivers and the environment in general,” points out Marcos Spitzner Filho, CFO of Packem.
Umasree’s CEO Punit Gopalka said he chose Packem because it is a young, energetic company with a future vision. In addition, he highlighted India as a strategic location to serve the global market, in which it has been operating since 2005 and, for the first time, with a 100 percent recycled and recyclable product.
The greatest innovation of recent years
Gopalka sees a lot of potential in the new product. “End users and governments are pressuring manufacturers to identify a new product that is environmentally sustainable,” he pointed out. The global FIBC market is led by five countries – India, China, Vietnam, Turkey and Mexico – which in 2021 exported 250 million units, with India accounting for 50 percent of that volume.
“We predict that at least 2 percent of the global big bag market will be able to replace the polypropylene product immediately with PET/PCR big bags and that this replacement will increase over the years,” Umasree’s CEO reckoned.
According to Packem, this is the greatest innovation of recent years in the segment of packaging for agriculture. “Packem’s goal is to develop the circular economy of packaging for the sector. These are the first 100 percent bag-to-bag projects in the world and will see the FIBCs used in the field processed and recycled to be made into big bags again. We will reuse 100 percent of the rPET big bags and this clearly demonstrates our commitment to eliminate virgin plastic from agribusiness and industry, using recycled plastic taken from farms and the environment as a whole,” highlighted Spitzner Filho.
The special technology for the production of high performance fabrics from polyester/PET PCR is exclusive to Austrian machine manufacturer Starlinger. Packem’s first sustainable big bag facility is located in Aurora (State of Santa Catarina), next to its current headquarters, with installed capacity to produce 6.4 million units of big bags a year.
Packem produces some 6 million big bags a year. With the rPET project, it will create more than 400 new direct jobs.
Based in Ahmedabad, Gujarat, Umasree has been providing customised FIBCs for more than 15 years. It produces 3.5 million units each year.