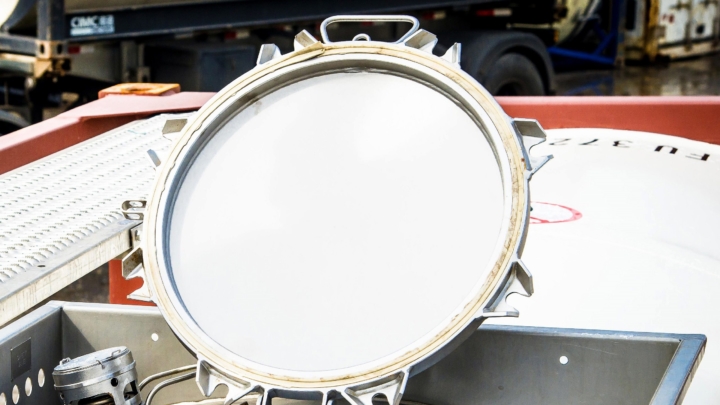
There are concerns over potential waste material degradation which could adversely affect the environment and health.
The review of PFAS materials is mostly being conducted by the European Chemicals Agency (ECHA), which implements EU chemicals regulations.
Certain restrictions, if enacted, would be detrimental to the tank container industry which mostly uses the material in its solid form for the manufacture of sealing elements. This is because alternative materials are less effective and could potentially reduce safety and increase waste.
Now ITCO has weighed in with a case study* of PFAS materials – particularly PTFE – outlining the critical role they play in safely transporting liquids and liquefied gases in bulk, most of which are classified as dangerous goods or are otherwise potentially hazardous.
The main detrimental uses considered by ECHA include: fire-fighting foam, textile treatment (eg, clothing), and food contact materials, such as food packaging.
ITCO says these industries use the material in vast quantities and their method of application is mobile and dispersible. The life expectancy is much shorter, and materials are disposed of in domestic waste systems.
Tank container sealing
In contrast, the material used for tank container sealing is in solid form and manufactured from rods of material. These do not shred into particles and do not cause the environmental issues cited in ECHA’s scope.
There is one sealing element is use, a man-lid braided PTFE seal, which is now recognised as a potential environmental risk and ITCO is currently advocating the removal of this seal from the list of acceptable seal elements. Even so, braided PTFE seals do not shed PFAS in the same manner as the items cited by ECHA and the production quantity is “infinitesimal” by comparison.
ITCO recognises the importance and supports the work of the governmental authorities, but believes that “the mobility, frequency, and degradability of sealing element materials, in the form that they are used within the tank container industry, is extremely low risk to the environment, compared to the material form cited by governmental research. Furthermore, by using the most appropriate materials for sealing elements, it prevents leakage of dangerous goods and protects the public and the environment.”
The study points out that highly regulated tanks, defined as UN Portable Tanks in the IMO International Dangerous Goods Code, rely on sealing elements within the valves, ancillaries and access hatches which are fitted to operational openings.
For some special applications, the tank and valve might also be lined. Sealing element materials must provide a range of technical properties that ensure the materials function as reliable and safe containment of liquids and liquefied gases.
PFAS, materials such as PTFE, are widely used because of the proven properties of chemical resistance, temperature range, durability, shrinkage, and vibration resistance, and cutting and machining qualities. Because of the exceptional properties of existing sealing elements, the operational safety and leak tightness record of the tank container remains excellent.
No alternative
Alternative sealing element materials have been researched and in some controlled applications have been trialled, but there is an “overwhelming technical need” to continue the use of solid form PFAS, it goes on.
“There is a risk to the environment and the public should access to the totally reliable existing sealing element material be restricted.”
As solid form PFAS used for sealing elements does not shred or degrade into particles, the seals have a long life expectancy and are eventually safely disposed as licensed industrial waste. ITCO has initiated a programme to consolidate used materials and to seek recycling options.
But for reasons of continued safety, ITCO is calling on regulators to designate solid PFAS sealing elements in tank containers as ‘materials of essential use’.
ITCO considers the danger and risks of the transport of chemical substances (flammable, toxic, corrosive dangerous goods) more hazardous than containment in static plant equipment.
Chemical plant valve sealing requirements are for mostly static operations and are within a controlled environment. The substances within a chemical plant would normally feature a bund to contain any leakage should this occur. It is possible to predict with greater accuracy the maintenance and emergency procedures because of the known environment.
Leak tightness
The consequences of leakages from tank containers can be significantly higher than leakages from valves in a controlled environment. “A leakage from portable tank containers in transit could result in dangerous and potentially lethal chemicals affecting the environment and the public with potentially serious consequences and a risk to life,” ITCO states.
Currently, and historically, the leak tightness record for portable tank containers operations is exceptional with very few reports of leakage due to design of the tank and its sealing elements.
But, moving away from PFAS-based materials without an equivalent alternative “will significantly increase the risk of leakage” either by reduction in the material’s sealing performance or significantly reducing the substance range of chemical compatibility, the study continues.
Alternative sealing elements could require to be chemical substance specific and require a lower safety margin for acceptable usages.
An appendix to a report following the meeting of the United Nations Working Party on the Transport of Dangerous Goods highlights the potential serious consequences for their safe transport presented by any restriction on the PFAS materials used in sealing. This reinforces ITCO’s concerns that restrictions in PFAS will result in a higher risk.
Life expectancy
In addition to the excellent sealing performance, existing materials have an extended life expectancy which benefits industry, its personnel, and the environment.
Because of their life expectancy, inherent durability, compatibility with almost all substances transported and in-situ cleanability, PFAS sealing elements also do not require frequent maintenance. This means that personnel are not required to strip and change valve seals frequently, and handle used and contaminated materials.
On the contrary, the use of alternative materials for sealing elements such as compressed fibrous gaskets, could requiring changing after each transport event, causing considerable handling of contaminated materials and an increase in the quantity of waste disposal.
Environment
It follows that the benefit of existing sealing element materials which have a long-life expectancy and wide chemical compatibility is that it reduces the frequency of sealing element maintenance replacement and therefore the quantity of new seals manufactured each year and the quantity disposed, ITCO argues.
New material from manufacturing off-cuts and machining and drillings can be recycled. However, used material recycling is currently problematic due to potential contaminants and the lack of a viable economic quantity of material. There is ongoing work to develop a viable process. For example, a trial recycling of tank container sealing elements is underway in the Netherlands.
Used tank container sealing element materials are currently safely disposed of through licensed industrial waste collection systems, but the aim is to increase recycling processes.
ITCO’s programme to dispose of sealing materials safely and to work with recyclers to develop processes to use the materials in a re-manufacture is also ongoing.
Recommendation
A restriction on PFAS would require finding technically suitable alternatives, manufacturing and testing these alternatives and then re-applying for industry approval.
But a tank container’s life expectancy exceeds 20 years and there are thousands of valve designs that are in continued use. “To re-approve all this equipment would take many years at significant cost; some valve designs might not achieve re-approval using non-PFAS alternatives. And achieving approval does not mean they will necessarily satisfy the customer’s end needs,” ITCO notes.
As a recommendation, ITCO is calling on regulators “for reasons of safety” to designate sealing elements in tank containers as “materials of essential use”. To this end, the organisation has submitted its arguments to ECHA, and will also soon pass it on to US Environmental Protection Agency (EPA) which is currently looking at PFAS forms that pose higher risks to water supplies.
*TG09 Case Study. The Health and Safety Impact on the Tank Container Industry in the event of a Restriction to the Manufacture of Perfluoroalkyl & Polyfluoroalkyl Substances (PFAS).